For several months, you’ve been working on a pilot project to develop or test new technology that can enhance your team’s operation of the production line. You’re constantly engaging with the testing team at a lighthouse facility, chosen specifically for its leadership support, technical expertise, and positive attitude towards the digital transformation in manufacturing.
The results are promising, and the feedback from the frontline team is excellent. Now, it’s time to scale. How quickly can we effectively implement the technology across all lines and facilities, unlocking the full potential demonstrated by the pilot? Addressing this question is crucial for manufacturing leadership, as technology deployment is a top priority to help overcome some of the challenges faced by the sector: labor shortage, high material costs and inflation, low productivity, among others.
According to the National Association of Manufacturers (NAM) 2022 4th Quarter outlook, more than 65% of organizations plan to continue investing in new equipment and technology, even in the event of an economic downturn. Another survey from the Manufacturing Leadership Council (MLC) indicates that 57% of respondents are experiencing small-scale AI pilot projects, and 28% are already implementing projects that have passed the pilot stage.
<< Read more: America’s (Other) Heroes: Manufacturers >>
Several elements impact an effective and rapid rollout of technology, ranging from budget constraints and infrastructure to technical support. However, one element that is often overlooked is the actual user, the frontline team, and how they will be guided to adopt the new ways of working. Not everyone is eager to change how they do things (in fact, most of us are not big fans of change), especially when the change is imposed.
Adopting new technologies in manufacturing
Older adults tend to be slower in adopting new technology, a trend corroborated by several studies. This is not ageism, as there are several factors that explain this: the older we are, the more accustomed we are to doing things a certain way; less exposure to some technology in our younger years and consequently, a lack of knowledge on how to use it and its benefits.
A literature research note published by the MIT AGELAB pointed out that multiple factors affect technology adoption, and the relevance of each factor varies for different social groups. According to the studies, older adults are more likely to adopt technology when they perceive its usefulness and potential benefit, rather than for mere novelty, like younger individuals.
<< Read more: Falconi Senior Partner and US MD is one of the Top 25 Consultants and Operations Leaders of 2024 >>
January 2024 data from the US Bureau of Labor Statistics (BLS) shows that 25% of the labor force is 55 years old or older, while almost 30% is 34 years old or younger. By analyzing these numbers, it’s possible to understand the relevance and challenge of technology deployment. Modernizing manufacturing jobs will make them more appealing to younger generations, which urges speed. However, we need to drive adoption through very different social groups, which urges caution. So, how can we effectively handle this process?
Benefits of the technology in manufacturing industry
Here are a few important things to keep in mind, assuming that the pilot has already proven the benefits of the technology:
- Build the right infrastructure: Getting basic things in place will enable the technology to be used safely. This includes high-speed Wi-Fi, charging stations for mobile devices, safe areas to access the devices, and computing power to quickly process a large amount of data.
- Ensure excellent technology usability: Resistance to change is natural, and people look for all kinds of excuses to avoid it, especially if they don’t like how the screens look or the response time to switch pages and refresh information.
- Secure local leadership support: Corporate support is beneficial, but it’s local leadership support that truly drives progress during this type of implementation. Having plant leadership communicate directly to the team about why this is important and what the benefits are will help to better illustrate the impact of the technology on their lives.
- Build local champions: Start with pilot lines and areas, even if you’ve already piloted the technology in other locations. This pilot mindset will show the local team that they are contributing to the development of the technology, which is true as you will likely uncover other opportunities for improvement. It will also help you build local champions, individuals who have experience with technology and can advocate for it among their peers.
- Be intentional about training and support: Develop easily accessible training materials and use various methods to transfer knowledge (reading, watching, trying). Also, define points of contact to support questions and create communities of practice, where people from similar social groups can interact and share their experiences.
Adopting practices and empathetic conversations boost tech implementation success
By adopting some of these practices, you will significantly increase your chances of success in this process. However, we will probably still hear things like “why bother, I’m retiring in 2 years” or “I prefer recording the machine setting on paper because it’s just easier for me”. When this happens, it’s important to take a human-centric approach and exercise empathy.
Investing in conversations that explore the benefits to the group tends to be very effective. Just as we don’t like change, we don’t like feeling that we are affecting the group’s performance, and being a good team player is always a good reason for change.
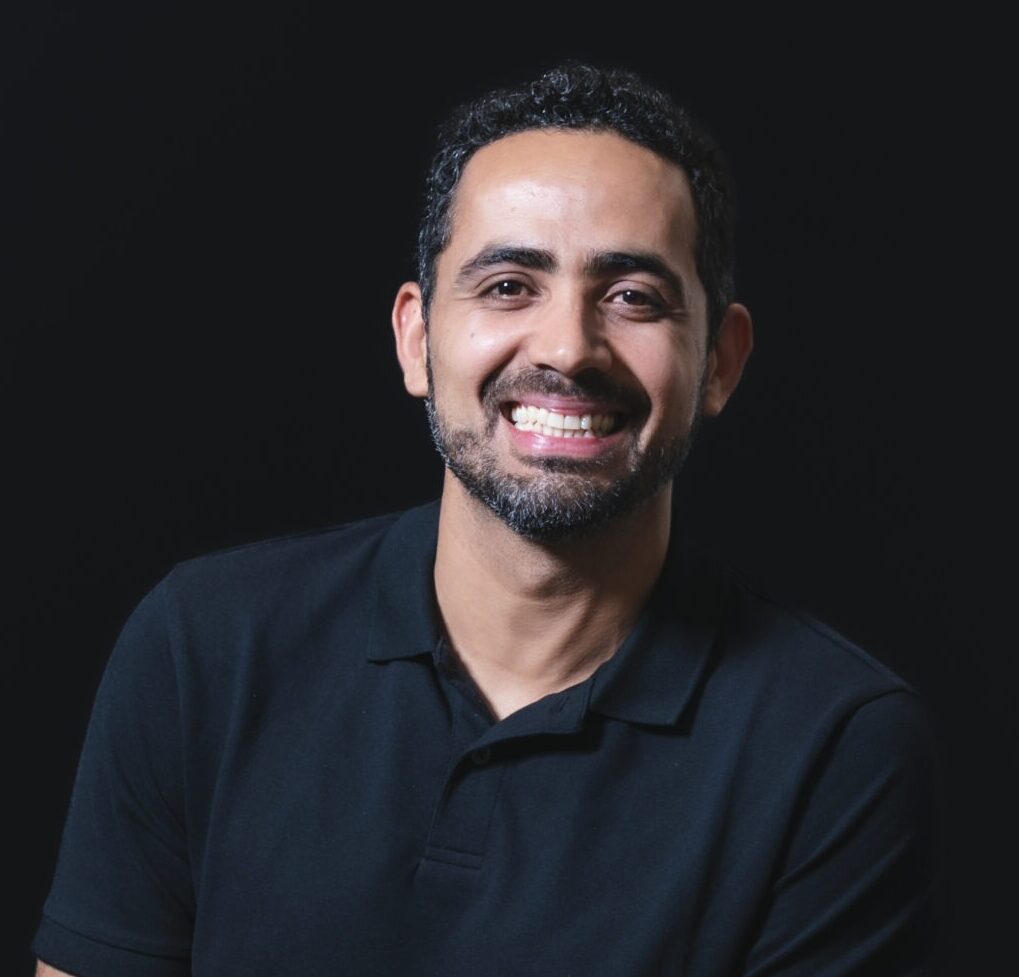
Gabriel Rodrigues