Supply chains have faced unprecedented challenges and disruptions since the onset of COVID-19. Five years later, some indicators suggest a return to normalcy, but the world has also changed significantly. New products, markets, suppliers, customers, technologies, and expectations have emerged, creating new opportunities and challenges for supply chain management.
How can you ensure that your supply chain is efficient and resilient in this new environment? How can you recapture the lost efficiencies and go beyond the pre-pandemic performance levels? In this article, we will share a simple approach for self-diagnosis that can help you identify and capture supply chain savings opportunities in six key areas.
<< Read more: 6 key steps to implement a successful manufacturing management system >>
A Simple Approach for Self-Diagnosis
If you already have a standardized S&OP process (Sales & Operations Planning) in place, you can use it as a starting point for your self-diagnosis. If not, you can check our other articles for how to get started. The six key areas to focus on are:
- Customer demand forecast: Have your customers’ order behavior changed and do you understand why? Improving accuracy by 5 – 10% can have a huge impact.
- Purchasing & Procurement: Do you have strong SLAs in place that dictate expected lead times and allow for flexibility in minimum order quantities (MOQs)? You should measure lead time performance and ensure it is consistent with your expectations.
- Production Scheduling: Do you have clear policies to prioritize orders and/or change orders? Measuring schedule adherence is another key metric that often explains poor supply chain efficiency.
- Inventory Accuracy & Policies: Are your inventory levels tracked real-time? Are they accurate? Do you have clearly defined safety stock levels and re-order points? It is important to not only track, but clearly and frequently communicate to your order management, purchasing and procurement teams so they know when to release orders to all internal and external stakeholders: suppliers and customers (external), as well as to manufacturing (internal).
- Resource Allocation: How much space, how many people, and how much (and which type of) equipment do you need to efficiently receive, put away, pick, and deliver materials to your production lines? The same question applies for packaging and shipping of your finished goods to customers.
- Technology Investments: Have you leveraged the latest technologies that can enhance your supply chain visibility, agility, and intelligence? Examples include artificial intelligence and machine learning, supply chain control towers, or blockchain technology.
Falconi Case: Automotive Supplier
To illustrate the potential of this approach, we will share a case study of an automotive supplier that we helped to identify $32M in supply chain savings opportunities in only six weeks. The opportunities were concentrated in two main areas:
Raw Materials Inventory
The company held a monthly average of $292M of raw materials inventory despite their desired levels of $184M, an excess of $108M (60% excess!).
<< Read more: Unlocking agile operational efficiency: challenges and rewards >>
To address this problem, we analyzed the safety stock policies, lead times and customer demand behavior. We found that the lead time assumptions within the safety stock tool had not been accurately adjusted for several quarters, resulting in over-ordering from suppliers with lead times greater than 84 days. A simple update of the lead time inputs used in the tool presented an opportunity to reduce excess raw materials inventories by $28M (26% of the total problem).
The remaining 74% of the excess inventory problem required more in-depth approaches, such as:
- Updating assumptions of appropriate safety stock levels by SKU
- Re-negotiating MOQ (minimum order quantities)
- Updating ASN (Advanced Shipping Notice) interfaces to track in-transit inventory
- Improving and integrating end-to-end S&OP processes
- Using advanced analytical models to more accurately predict demand
Warehouse Productivity
We also analyzed the warehouse productivity levels to test two hypotheses:
- Productivity levels had been negatively affected due to turnover and warehouse congestion.
- Warehouse congestion caused by excess raw material inventories was pushing overall headcount much higher than was necessary.
<< Read more: The role of warehouse efficiency in supply chain resilience >>
We used internal benchmarking logic to compare facilities and individual roles. This productivity benchmarking logic revealed an opportunity to reduce more than 50 headcount across facilities, representing a short-term opportunity of a 12% reduction. Considering the explosive growth for this particular company, this meant they could deliver 12% more product through their facilities without hiring additional personnel.
We defined a six-month roadmap with the company, the results of which would bring the company an exceptional payback of 30x without a single dollar invested in CAPEX.
As shown above, supply chain efficiency projects do not have to be complex, do not require excessive levels of CAPEX, and can be captured quickly. The key is having the knowledge and focus to quickly analyze and understand which link in your supply chain is holding efficiency back. From there, the solutions become very clear. If you are not satisfied with your current supply chain efficiency, we are available and willing to help! Contact us!
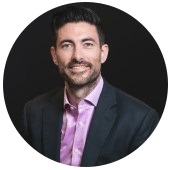
Matt McCabe
+14 years of experience that includes management systems, supply chain, maintenance, workforce optimization, and process transformation. Education: International Business from Loyola University and an MBA from IESE Business School in Barcelona.