Sports fans will be familiar with the saying, “The best ability is availability.” This feeling is certainly shared by manufacturing leaders and, albeit unknowingly, all company stakeholders including employees, customers, and even shareholders. A well-defined and executed maintenance strategy creates significant strategic advantages such as world class customer service levels, operational flexibility, increase in employee experience and, most obviously, a more profitable company. A poorly-defined and executed maintenance plan can create a ripple effect of chaos throughout the organization.
Cleaning and maintenance consume 40% of the operating budget
In 2020, 46.91% of surveyed companies in North America reported that they spent 21% to 40% of their operating budget on the cleaning and maintenance of their equipment and supplies (CMM, 2020). Is this good or bad? It depends. Are those resources being invested in equipment-monitoring devices to actively prevent maintenance issues, thus lifting production output, or are the same breakdowns and parts resurfacing each daily, shift, or even hour? The latter obviously consumes immense time and financial resources, not to mention the impact on overall productivity and employee morale.
<< Learn more: How AI transforms demand forecast accuracy and inventory optimization >>
It is well known that effective maintenance management is inextricably linked to operational efficiency. It is a main component of the commonly-used OEE (Overall Equipment Effectiveness) KPI. Yet, it is not enough to simply keep equipment running? Equipment operating outside optimum efficiency can lead to both throughout and quality issues. We hear many maintenance leaders oversimplify the causes of excessive unplanned downtime, putting the onus on ageing equipment or lack of time and resources. However, brand-new equipment, if not commissioned and managed properly, will wreak havoc on even the most modern, technologically-advanced production facilities.
Since 2009, 300 projects focused on Maintenance Management
Since 2009, Falconi has executed more than 6,000 projects, 300 of which focused on Maintenance Management. On average, across 20 industry sectors, Falconi has delivered an average return of more than 25% in maintenance productivity and cost. One such engagement in collaboration with a global steel manufacturer resulted in a 59% reduction in unplanned downtime in only five months. In fact, over the first three months, with quick wins actions, more than 35 hours of productive time was recovered.
<< Learn more: International consulting firm Falconi announces expansion with Chicago Office to serve North American clients and brings nearly four decades of proven results >>
To begin, an intensive analysis of current performance and identification of ‘bad actors’ responsible for more than 70% of unplanned downtime was executed. Followed by establishment of the basics: performance and routine adherence KPIs, critical inspection routes, planning and scheduling processes. Next, root cause analysis training (classroom and on-the-job), and standards development and one-the-job training for the top-5 most common repairs was executed. Finally, critical inventory levels and a 5S overhaul of the spare parts storeroom were implemented.
Even back in 2020, a survey found than 48% of respondents planned to or were currently using technology to capture machine data (PlantEngineering). This promising technology provides an easier path to a Predictive Maintenance strategy… even for companies with older equipment! Falconi recent deployed this strategy with a global food manufacturer, installing Internet of Things (IoT) devices to automate OEE measurement and capture performance parameters of production equipment. Analyzing newly available data, we reable to test different machine settings and refine machine learning algorithms, building the effective machine settings into the plant’s daily routine. Based on the reduction of downtime, resulting in a 24% increase in OEE and $USD 25M (million) EBITDA, Falconi trained the local team to analyze and use the data and personalized software, and sustain the improvements.
<< Learn more: What can digital transformation teach companies? >>
Are you ready to to turn effective maintenance management into a estrategic advantage? Whether you are taking your first steps or need the extra muscle to accelerate your current initiatives, Falconi has the experience, knowledge, and leading-edge technology to design and implement a transformative maintenance strategy. Contact our team to get started. Not ready to ask for external support? There are other ways we can help. Visit our website, sign up for our newsletter, or consult one of Falconi’s many publications.
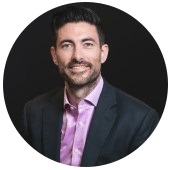
Matt McCabe