“Made in the USA.” Once a sign of a high-quality, durable product, the relentless pursuit of lower consumer prices led to globalization and, consequently, far fewer proud “Made in the USA” labels. Are we about to see this trend reversed? While American consumption of internationally produced goods is virtually guaranteed to persist, supply chain disruptions, geopolitical issues, and government investment suggest we will see more manufacturing come “home” (or at least closer to home).
Whether your own company, or others in your industry, are considering reshoring or nearshoring, it’s likely that competition for customers, employees, and even shareholders is going to intensify.
Are you prepared to win?
How can you maximize this opportunity?
In a somewhat oversimplified definition, manufacturers convert inputs in the form of raw materials into affordable products that consumers or other businesses need. So, what’s so challenging about it? Let’s explain through a breakdown of functional domains within a manufacturing facility.
- Production: Maximizing volume and speed.
- Maintenance & Engineering: Keeping equipment healthy and implementing new equipment.
- Quality: Minimizing defects.
- Operational Performance: Monitoring KPIs and their connection to financial results.
- Supply Chain: Purchasing and delivering materials on time to production lines.
- Continuous Improvement: Identifying and prioritizing actions to improve results.
- Health & Safety: Striving for zero incidents or injuries.
- People: Recruitment, training, development, and retention of employees.
- Management & Leadership: Technical knowledge, experience and people skills.
- Technology: Automation, analytics, sensors (IoT), etc.
Successful integration of the functional domains usually falls squarely on the shoulders of Plant Managers. Do you have a newfound respect for our great American manufacturers yet?
<< Learn more: Driving success in the industry: the power of process mining >>
Management: bringing the pieces together
Every manufacturer has opportunities for improvement across their functional domains. Falconi has supported 100 global manufacturers to refocus, redesign, or build their “Manufacturing Management Systems” from scratch. One food & beverage manufacturer generated significant benefits from our approach and their leadership’s commitment. Let’s look at the main steps:
Step 1: Performance analysis to establish a connection between KPIs and financial results in every functional domain revealed improvement opportunities.
Step 2: Defining processes and specific critical tasks and their associated work instructions.
Step 3: Updating the standards and execution of short, isolated pilots to ensure results were positively impacted.
Step 4: Validation and sign-off of new standards.
Step 5: Retraining of employees and managers with follow-up coaching as new ways of working were implemented across the business.
Step 6: Functional, Regional, and Global results were tracked, and ineffective standards were refined.
Step 7: Handoff to functional domain “Owners” responsible for ongoing monitoring and performance.
<< Learn more: 4 steps to harness potential of Value-Based Budgeting in the tech industry >>
Through this approach, we were able to implement a new Management System in 70+ manufacturing plants, achieving global consolidated improvements of a 3% Overall Equipment Effectiveness increase, a 7% decrease in Quality Losses, and an 11% reduction in Utilities Consumption.
Technology trends in management systems
Three common technology applications support management system sustainment.
Analytics: Generation of real-time results usefully in the form of performance dashboards accessible to those who execute the work. This enables immediate identification and resolution of issues.
Automation: If capital expenditure (CAPEX) budgets are available, automation can be applied to parts of the production process that require extreme precision, are no longer deemed safe to be done by humans, or to provide a more ergonomic solution for employees (heavy lifting, twisting, turning, etc.).
Generative AI: A new entrant earn the attention of leaders for its ability to assist with work instructions, troubleshoot equipment issues, or tasks which require the interpretation of data.
Common Shortfalls
Despite perpetual improvement opportunities in all domains, we see companies struggle with Continuous Improvement, People, and Technology. These are nothing to be ashamed of and often require an honest reevaluation of your management system. In many cases, a quick diagnosis or outside opinion can bring fresh new perspectives.
<< Learn more: Optimizing maintenance efficiency: unlocking the true potential of operations >>
Whether taking it upon yourself to advance your operational excellence journey or requesting outside help, problems are to be celebrated and attacked, not ignored. Have you taken an look at your management system? Even if reshoring or nearshoring forecasts fall short of a full american manufacturing renaissance, it pays to be prepared. What do you go do to excel in the next years?
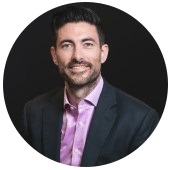
Matt McCabe