As we approach 2025, the manufacturing industry faces an evolving landscape shaped by complex market constraints and heightened demands. Companies are struggling with supply chain disruptions, increasing labor costs, energy prices, sustainability regulations, and shifting customer expectations.
These dynamics are driving an urgent need for manufacturers to rethink their traditional approaches and embrace digital transformation as a catalyst for change. To thrive in this environment, manufacturers must prioritize transparency, agility, and real-time decision-making to stay competitive and resilient.
Key result areas such as optimizing production efficiency, reducing operational losses, and achieving consistency in product quality are top priorities to increase performance efficiently.
<< Read more: Benefits of digital transformation in manufacturing industry >>
Challenges and roadblocks manufacturing may face in 2025
Despite the vast potential of digital transformation, manufacturing companies face several challenges that threaten to derail their progress, such as:
Lack of operational data visibility: Overall Equipment Effectiveness (OEE) and yield losses often arise from a lack of transparency in machine stoppages and variations in process efficiency, which requires more accurate and comprehensive data.
Siloed digital initiatives: varied manufacturing systems and inconsistent infrastructure readiness across plants are barriers to scaling digital initiatives, resulting in longer proof-of-concept periods and validation delays.
Skill gaps and resistance to change: the rapid evolution of digital technologies is creating a generational and skill gap on the shop floor and the high turnover of skilled talent makes it challenging to retain knowledge and ensure continuity.
Sustainability and cost pressures: varying utilities consumption and the need for more sustainable resource management are becoming operational concerns.
Overcoming challenges through digital enablers
Manufacturers should focus on building a solid foundation for their digital journey to overcome these obstacles. Firstly, it is important to establish a dedicated digital governance team with a clear vision of the company’s digital future.
One aspect that cannot be overlooked is that digital transformation must be fully integrated into the company’s operational routines and practices. Furthermore, change management strategies should focus on building the necessary capabilities, promoting acceptance, and fostering digital fluency among all employees.
<< Read more: America’s (Other) Heroes: Manufacturers >>
Achieving success in manufacturing
Embracing digital transformation is not optional anymore but a must for companies wanting to drive sustainable growth. By understanding market constraints and focusing on key result areas, manufacturers can navigate challenges effectively.
The first change is to adopt a problem-centric approach, prioritizing the solution of operational or business problems over merely adopting technology for its own sake. It is also important to choose pilot plants or lines that have demonstrated strong maturity in their management systems. They should serve as testing grounds for digital initiatives, with a focus on achieving measurable outcomes and scaling up.
Continuing the process, conduct controlled pilots to test digital solutions and measure tangible and intangible returns. Then evaluate and manage the readiness of all infrastructure elements, including the physical condition of plants, the availability of necessary devices and equipment, and the connectivity required to support real-time data transfers.
Finally, don’t forget to prioritize the capture of high-quality data, focusing on accuracy, consistency, and relevance. Embracing digital transformation is not just about technology — it’s about rethinking how to achieve results and unlocking new opportunities to lead in the manufacturing industry.
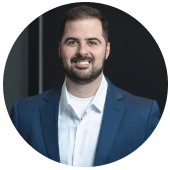
Henrique Melillo